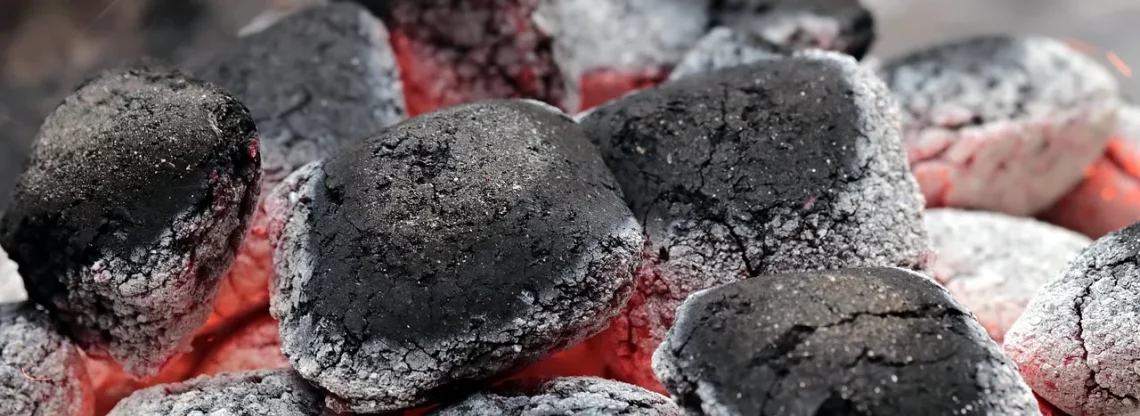
Understanding the Cost of Carbon Fiber: A Comprehensive Guide
Understanding the Cost of Carbon Fiber: A Comprehensive Guide
The demand for advanced materials in various industries has led to a surge in interest in carbon fiber. Known for its remarkable strength-to-weight ratio and versatility, carbon fiber is increasingly being utilized in sectors ranging from aerospace to automotive, sports equipment, and even fashion. With the growing adoption of this material, understanding the cost associated with carbon fiber becomes imperative for manufacturers, consumers, and investors alike.
Carbon fiber is not just about the material itself; it encompasses a whole ecosystem of production processes, supply chains, and technological advancements that influence pricing. Factors such as raw material costs, manufacturing techniques, and market demand all play crucial roles in determining the final price of carbon fiber products. As industries continue to push for lighter and stronger materials, the understanding of these cost factors becomes essential for making informed decisions.
Whether you are an engineer looking to incorporate carbon fiber into your designs, a business owner assessing material costs, or a curious consumer wanting to learn more, grasping the nuances of carbon fiber pricing can provide valuable insights. This guide aims to unravel the complexities surrounding the cost of carbon fiber and offer a clearer picture of its financial implications across various applications.
The Raw Materials Behind Carbon Fiber
Understanding the cost of carbon fiber begins with examining its raw materials. Carbon fiber is primarily made from polyacrylonitrile (PAN), a synthetic polymer that is spun into fibers and then treated to create the final product. The quality of the PAN used is a major factor affecting the overall cost of carbon fiber. High-quality PAN can lead to stronger and lighter fibers, but it is also more expensive.
Another significant raw material is pitch, which can also be used to produce carbon fibers, although it is less common. The choice of material impacts not only the properties of the final product but also the cost structure. PAN-based fibers are generally considered superior in terms of performance, but they come at a higher price point compared to pitch-based fibers.
The sourcing of these raw materials also affects costs. Fluctuations in the oil market, for example, can influence the price of PAN since it is derived from petroleum products. Moreover, the environmental and regulatory factors surrounding the production of these materials can lead to additional costs that manufacturers must account for. As industries increasingly focus on sustainability, the transition to bio-based alternatives could alter the cost landscape, making it a critical factor to monitor.
In addition, the supply chain plays a vital role in determining the accessibility and pricing of raw materials. Disruptions in supply chains, whether due to geopolitical issues or natural disasters, can lead to sudden spikes in costs. Thus, anyone interested in carbon fiber must keep an eye on both the raw materials and the broader supply chain dynamics to understand the pricing fully.
Manufacturing Processes and Their Impact on Pricing
The manufacturing process of carbon fiber is intricate and labor-intensive, which significantly contributes to its cost. The production involves several stages, including spinning, stabilization, carbonization, surface treatment, and sizing. Each of these steps requires specialized equipment and skilled labor, leading to higher operational costs.
The spinning process, where PAN or pitch is drawn into fibers, is critical for determining the quality of the final product. Higher precision in this stage can lead to better mechanical properties but at an increased manufacturing cost. Following spinning, the stabilization process involves heating the fibers in air to convert them into a more thermally stable form. This step is essential, as it affects the overall structure and properties of the carbon fibers.
Carbonization, the actual conversion of stabilized fibers into carbon fibers, is where the bulk of the energy consumption occurs. This phase requires high temperatures, often exceeding 1,000 degrees Celsius, which translates into substantial energy costs. Manufacturers that invest in energy-efficient technologies may offset some of these costs, but the initial investment can be significant.
Surface treatment and sizing are also crucial for the fibers’ compatibility with resins in composite applications. These processes add to the overall cost but are necessary to ensure that the carbon fibers perform effectively in their intended applications.
Moreover, advancements in manufacturing technologies, such as automated fiber placement and 3D printing, have the potential to reduce costs in the long run. However, the transition to these new technologies requires upfront investment that may not be feasible for all manufacturers. Understanding these manufacturing nuances is essential for anyone evaluating the cost of carbon fiber, as they can significantly influence the pricing structure.
Market Demand and Its Influence on Carbon Fiber Pricing
Market demand is perhaps the most dynamic factor influencing the cost of carbon fiber. As industries evolve, the applications for carbon fiber continue to expand, driving demand across various sectors. The aerospace and automotive industries have been particularly influential in this regard, as they increasingly seek lightweight materials to enhance fuel efficiency and performance.
The rising popularity of electric vehicles (EVs) has further amplified the demand for carbon fiber. Manufacturers are looking for materials that can offset the weight of heavy batteries while maintaining structural integrity. This has created a surge in orders for carbon fiber components, which can lead to price increases due to heightened demand.
In addition to traditional applications, the growing interest in consumer products—such as bicycles, sporting goods, and even fashion items—has broadened the market landscape. As more companies venture into carbon fiber manufacturing, competition can help stabilize prices. However, if demand continues to outstrip supply, prices may rise.
Another important aspect of market demand is the influence of innovation. As new applications are developed and existing technologies are improved, the utility of carbon fiber expands. For instance, advancements in recycling processes may lead to the emergence of recycled carbon fiber, which could offer a cost-effective alternative and impact pricing dynamics.
Global economic conditions also play a pivotal role in shaping market demand. Economic downturns can reduce spending in sectors that utilize carbon fiber, leading to a decline in demand and potentially lowering prices. Conversely, economic booms can drive up demand, causing costs to surge.
Understanding market demand is crucial for manufacturers and consumers alike, as it provides insight into potential pricing trends and helps in making informed decisions about investments in carbon fiber technologies.
Conclusion: Balancing Cost and Value in Carbon Fiber
In summary, the cost of carbon fiber is influenced by a multitude of factors, including raw material prices, manufacturing processes, and market demand. For those involved in industries where carbon fiber is utilized, understanding these elements is essential for making informed choices about material selection and budget allocation.
While the initial costs of carbon fiber can be higher compared to traditional materials, the long-term benefits—such as increased durability, reduced weight, and enhanced performance—can often justify the investment. As technology continues to advance and the market for carbon fiber evolves, ongoing assessment of these factors will be vital for stakeholders.
Ultimately, balancing cost with the value that carbon fiber provides is key. By staying informed about the intricacies of pricing, industry professionals can navigate the complexities of the carbon fiber landscape more effectively, ensuring that they leverage this remarkable material to its full potential.

