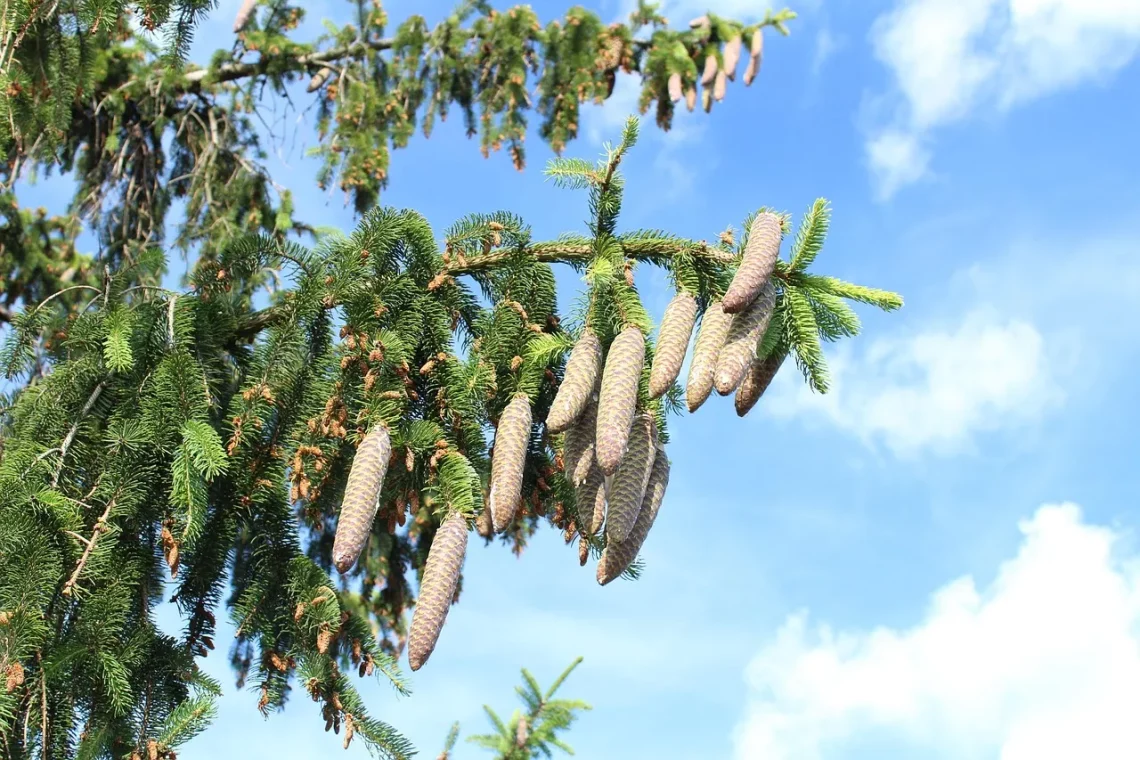
Understanding Small Cone Shaped Bump Stops and Their Applications
Understanding the dynamic world of bump stops is essential for various industries, especially in automotive and manufacturing sectors. These small cone-shaped components play a crucial role in cushioning and controlling the motion of moving parts. Their design, often overlooked, is fundamental in ensuring safety, stability, and efficiency in machinery and vehicles.
Bump stops work by absorbing shock and preventing damage during movement. They are strategically placed within systems to limit the range of motion, providing a fail-safe mechanism that protects against excessive force or impact. The significance of these small components cannot be underestimated, as they contribute not only to the longevity of machinery but also to the overall performance of vehicles.
As industries evolve and technology advances, the applications of bump stops continue to diversify. From enhancing ride quality in automobiles to providing essential cushioning in industrial equipment, their utility is vast. Understanding their design, function, and applications is vital for engineers, manufacturers, and anyone involved in product development. The following sections will delve deeper into these aspects, exploring the various types of bump stops, their characteristics, and their specific applications across different sectors.
Types of Bump Stops and Their Characteristics
Bump stops come in various shapes and sizes, each designed to meet specific requirements in different applications. The most commonly used materials for bump stops include rubber, polyurethane, and even metal in some specialized cases. Each material has its unique properties that affect performance, durability, and cost.
Rubber bump stops are popular due to their excellent shock-absorbing capabilities. They are flexible and can withstand prolonged use without significant wear. Their elasticity allows them to compress and expand under force, making them ideal for automotive applications where they can absorb impacts from road irregularities.
Polyurethane bump stops, on the other hand, offer enhanced durability and resistance to environmental factors such as oil, chemicals, and temperature fluctuations. They are often used in industrial settings where exposure to harsh conditions is common. The rigidity of polyurethane allows for a more controlled compression, making them suitable for heavy machinery that requires precise motion control.
Metal bump stops are less common but are utilized in high-load applications where extreme durability is necessary. They can withstand significant impact forces and are typically used in heavy-duty trucks or construction equipment. However, they lack the cushioning properties of rubber and polyurethane, which can lead to greater wear and tear on connected components.
In addition to material differences, bump stops can also vary in shape and size. Cone-shaped bump stops are particularly effective due to their tapered design, which allows for gradual compression. This design helps distribute the force evenly, reducing the risk of damage to the components they protect. The size of the bump stop must also be carefully considered, as a larger bump stop may provide more cushioning but could limit the range of motion more than desired.
Overall, the choice of bump stop type and material is critical in ensuring the safety and efficiency of the application. Understanding these characteristics helps engineers and manufacturers select the appropriate bump stop for their specific needs.
Applications of Bump Stops in Automotive Engineering
In automotive engineering, bump stops play a crucial role in ensuring vehicle stability and comfort. They are typically installed in suspension systems, where they act as a buffer between the vehicle’s chassis and the axle. This positioning allows them to absorb shocks from bumps and uneven surfaces, preventing excessive jarring that could lead to damage or discomfort for passengers.
One of the primary functions of bump stops in vehicles is to limit suspension travel. When a vehicle encounters a large bump or dip, the suspension system compresses. If this compression exceeds a certain limit, the bump stop engages, preventing the suspension from bottoming out. This engagement protects critical components such as shocks and struts from damage, prolonging their lifespan and ensuring a smoother ride.
Additionally, bump stops are essential in maintaining vehicle alignment. When the suspension compresses excessively, it can throw the vehicle’s alignment off, leading to uneven tire wear and handling issues. By providing a controlled limit to suspension movement, bump stops help maintain proper alignment, ensuring that vehicles handle predictably and safely.
Bump stops are also utilized in off-road vehicles, where the terrain can be particularly challenging. In these applications, robust bump stops are necessary to withstand the increased forces from rough terrain. They help ensure that the vehicle can navigate obstacles without sustaining damage, allowing for a more enjoyable off-road experience.
In summary, the applications of bump stops in automotive engineering are extensive and vital for vehicle performance. They contribute to safety, comfort, and longevity, making them an essential component of modern vehicles.
Importance of Bump Stops in Industrial Equipment
Bump stops are not limited to automotive applications; they also play a significant role in various types of industrial equipment. In manufacturing and machinery, bump stops are employed to protect components from excessive impact and wear. Their application can be seen in conveyor systems, robotics, and heavy machinery.
In conveyor systems, bump stops are used to absorb the impact of materials being transported. Heavy loads can create significant forces when they come to a sudden stop. Without bump stops, these forces could lead to equipment failure or product damage. By incorporating bump stops, manufacturers can enhance the longevity of their conveyor systems and ensure smoother operations.
Robotics is another area where bump stops are essential. In robotic arms and automated systems, precise movement is crucial. Bump stops help control the range of motion, preventing the robotic components from colliding with one another or with the environment. This control not only protects the machinery but also enhances the accuracy of operations, leading to improved productivity.
Heavy machinery, such as excavators and forklifts, also benefits from the incorporation of bump stops. These machines often operate under extreme conditions and face considerable forces during operation. Bump stops provide an additional layer of protection, absorbing shocks that could otherwise lead to mechanical failure or accidents.
Furthermore, the use of bump stops in industrial applications can contribute to worker safety. By preventing unexpected movements and impacts, they help create a safer working environment. This aspect is particularly important in environments where workers are in close proximity to heavy machinery.
In conclusion, the importance of bump stops in industrial equipment cannot be overstated. They enhance performance, protect machinery, and contribute to worker safety, making them an invaluable component in various industrial applications.
Future Trends in Bump Stop Technology
As technology continues to advance, the future of bump stop design and application is poised for innovation. With the increasing focus on efficiency and sustainability, manufacturers are exploring new materials and designs that offer enhanced performance and reduced environmental impact.
One promising trend is the development of smart bump stops equipped with sensors. These advanced components could provide real-time data on the forces experienced during operation, allowing for better monitoring and adjustments. Such technology could lead to more responsive systems that adapt to varying conditions, further improving safety and performance.
Additionally, there is a growing emphasis on environmentally friendly materials. Manufacturers are increasingly looking to sustainable alternatives to traditional rubber and polyurethane. Biodegradable materials or those sourced from renewable resources could reduce the environmental footprint of bump stops.
The integration of 3D printing technology is also expected to revolutionize the production of bump stops. This technology allows for rapid prototyping and customization, enabling manufacturers to produce components tailored to specific applications. This flexibility can lead to improved performance and cost savings.
Finally, as industries continue to prioritize automation and robotics, the demand for sophisticated bump stops will likely increase. These components will need to evolve to meet the needs of advanced machinery, ensuring safety and efficiency in increasingly complex systems.
In summary, the future of bump stop technology is bright, with numerous opportunities for innovation. By embracing new materials, designs, and technologies, manufacturers can enhance the performance and sustainability of these essential components.
In conclusion, bump stops are vital components across various applications, ranging from automotive to industrial machinery. Their role in protecting components and ensuring safety cannot be overlooked. As technology progresses, the potential for enhancing bump stop design and function remains significant, paving the way for improved efficiency and sustainability in the years to come.

