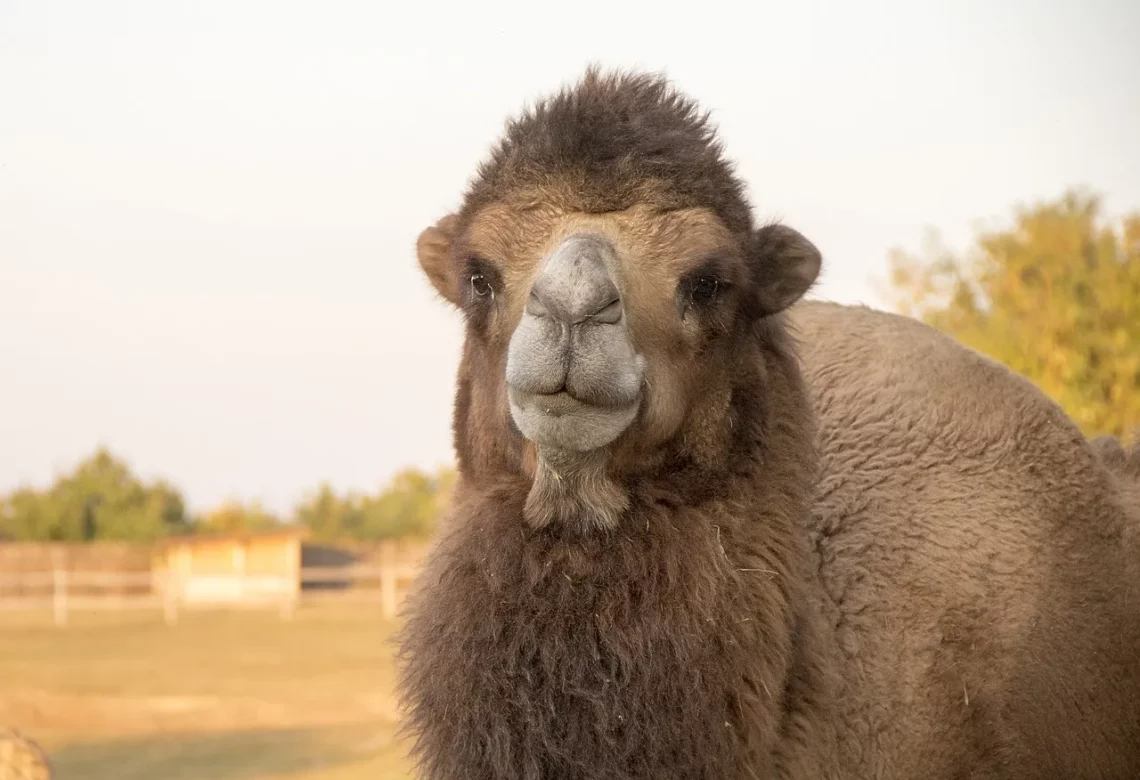
Understanding Small Cone Shaped Bump Stops and Their Applications
Understanding the intricacies of small cone-shaped bump stops can greatly enhance our comprehension of their significance in various applications, particularly in the automotive and industrial sectors. These seemingly simple components play a crucial role in cushioning and absorbing impacts, ensuring that machinery and vehicles operate smoothly while minimizing wear and tear. As technology advances, the materials and designs of bump stops have evolved, leading to improved performance and durability.
Cone-shaped bump stops are strategically engineered to provide optimal support and impact resistance. Their unique shape allows for effective energy absorption, which is vital in numerous scenarios, from automotive suspensions to industrial machinery. The functionality of these bump stops not only contributes to the longevity of equipment but also enhances safety by preventing unexpected failures.
In a world where efficiency and reliability are paramount, understanding how small cone-shaped bump stops work can empower engineers and mechanics to make informed decisions about their applications. Choosing the right bump stop can significantly influence the performance of a vehicle or machine, making it essential for professionals to grasp the nuances of these components. This article delves into the characteristics, functions, and applications of small cone-shaped bump stops, shedding light on their importance in various fields.
Characteristics of Small Cone-Shaped Bump Stops
Small cone-shaped bump stops are designed with specific characteristics that set them apart from other types of bump stops. Their conical shape is not merely aesthetic; it serves multiple functional purposes. The tapering form allows for gradual compression, which helps in distributing the load evenly when an impact occurs. This feature is particularly beneficial in reducing shock loads and prolonging the lifespan of the components they are integrated into.
Material selection is another critical aspect of the design of these bump stops. Most small cone-shaped bump stops are made from rubber, polyurethane, or other resilient materials that offer excellent elasticity and durability. These materials are chosen not only for their shock-absorbing capabilities but also for their ability to withstand harsh environmental conditions, such as extreme temperatures and exposure to chemicals.
Moreover, the size and hardness of the bump stops can be customized to meet specific application requirements. For instance, softer bump stops may be used in applications where more cushioning is necessary, while harder variants can provide firmer support in heavy-duty environments. This versatility makes small cone-shaped bump stops suitable for a wide range of applications, from automotive suspensions to industrial machinery.
Another noteworthy characteristic is their ease of installation. Most bump stops are designed for straightforward mounting, allowing for quick replacements and upgrades. This feature is particularly advantageous in industries where downtime needs to be minimized, and efficiency is critical.
In essence, the unique characteristics of small cone-shaped bump stops make them indispensable in many sectors. Their ability to absorb shock, coupled with their durable materials and customizable features, ensures that they remain a preferred choice for engineers and mechanics alike.
Applications in Automotive Suspension Systems
In the automotive industry, small cone-shaped bump stops play a pivotal role in suspension systems. They serve as a final line of defense against bottoming out, which can occur when the suspension reaches its limit of travel. When a vehicle hits a bump or pothole, the suspension compresses, and the bump stop engages to prevent the suspension components from making direct contact with one another. This engagement helps to minimize noise, vibration, and harshness, ultimately providing a smoother ride for passengers.
The design of these bump stops allows for progressive compression. As the bump stop compresses, it gradually increases resistance, which helps to cushion the impact. This characteristic is crucial for maintaining vehicle stability, especially during sudden maneuvers or when traversing uneven terrain.
Additionally, small cone-shaped bump stops can be found in various types of vehicles, from sedans to off-road trucks. Their ability to adapt to different weight distributions and suspension configurations makes them an essential component across a broad spectrum of automotive designs. They are often used in conjunction with other suspension components, such as shock absorbers and springs, to create a harmonious system that enhances vehicle performance.
In high-performance vehicles, the choice of bump stop can significantly influence handling and ride quality. Manufacturers often invest in advanced bump stop designs that incorporate multiple materials or unique geometries to optimize performance. This focus on quality and functionality exemplifies the importance of small cone-shaped bump stops in achieving superior automotive engineering.
Overall, their critical role in automotive suspension systems underscores the necessity of understanding and selecting the appropriate bump stops for specific vehicle applications. Properly functioning bump stops not only enhance ride quality but also contribute to overall vehicle safety and longevity.
Industrial Uses and Benefits
Beyond the automotive sector, small cone-shaped bump stops are extensively utilized in industrial applications. These components are found in various machinery and equipment where impact protection is required. For instance, they are commonly used in forklifts, conveyor systems, and production equipment to absorb shocks and prevent damage during operation.
In industrial environments, equipment is often subjected to heavy loads and continuous wear. The presence of bump stops helps to mitigate the effects of these forces by providing a cushioning effect that reduces stress on critical components. This function is particularly important in high-speed machinery, where even minor impacts can lead to significant wear and potential failures.
Another benefit of using small cone-shaped bump stops in industrial applications is their ability to minimize noise and vibration. Machinery often generates excessive noise during operation, which can lead to an uncomfortable work environment. By incorporating bump stops, manufacturers can significantly reduce the noise levels produced by machinery, creating a more pleasant workspace for employees.
Additionally, the versatility of small cone-shaped bump stops allows them to be tailored for specific industrial needs. Custom sizes, hardness levels, and materials can be engineered to meet the unique demands of different machines. This adaptability ensures that businesses can find suitable solutions for their equipment, enhancing overall operational efficiency.
Moreover, incorporating bump stops into machinery design can lead to cost savings in the long run. By reducing wear and tear on components, businesses can extend the lifespan of their equipment, leading to fewer replacements and lower maintenance costs. This aspect is particularly appealing for industries where operational efficiency and cost-effectiveness are paramount.
In summary, small cone-shaped bump stops serve a vital function in various industrial applications, providing impact protection, noise reduction, and increased equipment longevity. Their adaptability and performance make them an essential component in modern machinery.
Choosing the Right Bump Stop for Your Needs
Selecting the appropriate small cone-shaped bump stop for a specific application requires careful consideration of several factors. First and foremost, it is essential to evaluate the intended use and the specific requirements of the machinery or vehicle. Different applications will demand varying levels of cushioning, durability, and resistance to environmental conditions.
Understanding the load that the bump stop will need to support is crucial. This includes considering the weight of the vehicle or machinery, as well as any dynamic forces that may be present during operation. For heavier applications, a firmer bump stop may be necessary to provide adequate support, while lighter applications may benefit from softer, more forgiving materials.
Another key factor to consider is the environmental conditions in which the bump stop will operate. Exposure to extreme temperatures, moisture, or chemicals can significantly affect the performance of the material. It’s essential to select bump stops made from materials specifically designed to withstand such conditions to ensure long-lasting performance.
Additionally, installation requirements should be taken into account. Some bump stops may require specialized mounting hardware or specific installation techniques, while others may be designed for easy replacement. Understanding the installation process can help streamline maintenance and reduce downtime in industrial settings.
Finally, consulting with manufacturers or industry experts can provide valuable insights into the best bump stop options for specific applications. With the right information and resources, engineers and mechanics can make informed decisions that optimize performance and enhance the longevity of their equipment.
In conclusion, the selection process for small cone-shaped bump stops is multifaceted and should be approached with careful consideration of application needs, material properties, and installation requirements.
This article is for informational purposes only and should not be considered medical advice. For any health-related issues, please consult a qualified healthcare professional.

