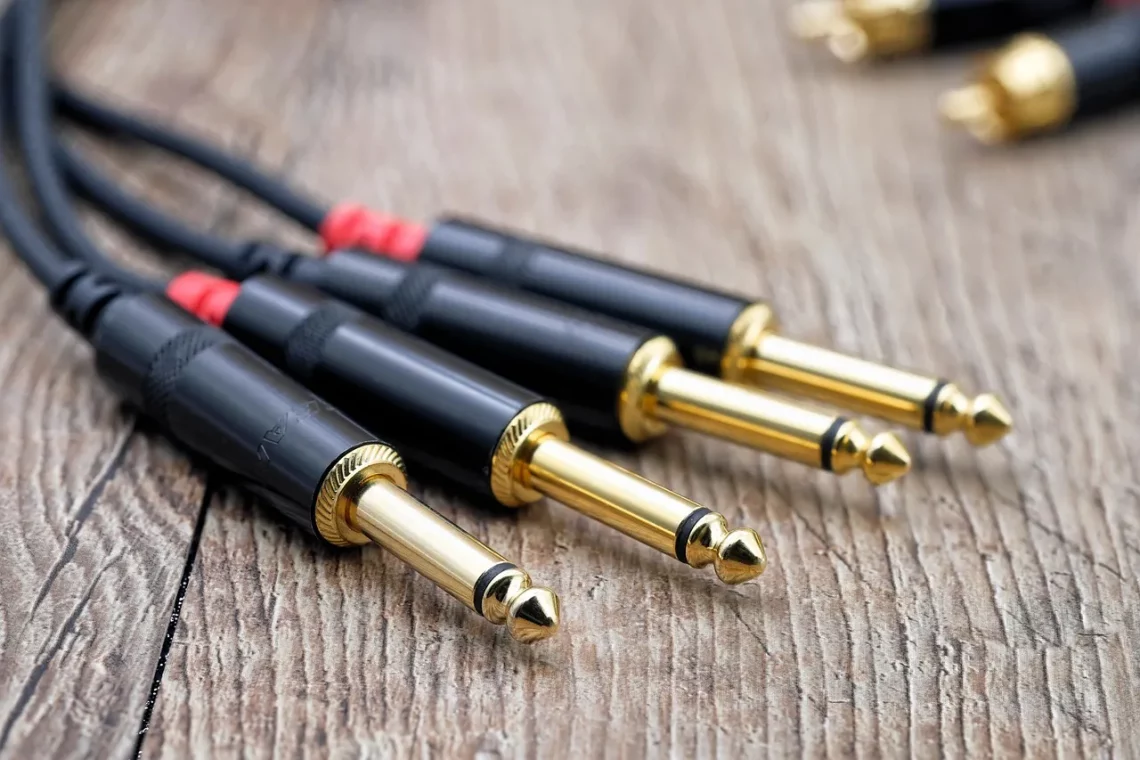
Understanding Push Pull Cables: Functions and Applications Explained
Understanding push-pull cables is essential for anyone involved in mechanical engineering, automotive design, or even recreational vehicle modifications. These versatile components play a crucial role in various applications, enabling smooth and precise control of different systems. Push-pull cables are typically used to transfer motion, allowing operators to engage or disengage mechanisms seamlessly, which enhances both functionality and safety.
The design of push-pull cables can vary, but they generally consist of a flexible sheath containing a cable that can be pushed or pulled to transmit force. This dual functionality sets them apart from other types of control cables, which may only serve one purpose. As such, understanding their structure and operation can lead to better application and implementation in numerous fields.
Moreover, as industries evolve and technology advances, the demand for efficient and reliable push-pull cables continues to grow. From automotive systems to industrial machinery, these cables are foundational components that contribute to the overall effectiveness of many operations. By exploring the intricacies of push-pull cables, we can appreciate their significance and the diverse applications they serve.
How Push Pull Cables Work
Push-pull cables operate on a straightforward principle: they convert linear motion into mechanical movement. The basic structure of a push-pull cable consists of a flexible outer sheath and an inner cable that can slide freely within it. When an operator pushes or pulls on one end of the cable, the inner cable moves correspondingly, transferring that motion to the other end.
The mechanism is relatively simple, yet it can be utilized in various complex applications. In many cases, push-pull cables are employed in situations where precise control is necessary, such as in throttle controls for vehicles or in the activation of machinery. The ability to push and pull allows for a wide range of motions, making them suitable for applications that require both engagement and disengagement.
The materials used in the construction of push-pull cables are critical to their performance. They are often made from durable metals or high-strength synthetic materials to withstand wear and tear. Additionally, the design of the cable’s end fittings—such as eyelets, hooks, or clevises—can significantly impact how they connect to the systems they control. Proper installation and maintenance are essential to ensure that these cables operate smoothly and safely.
Understanding how push-pull cables work is vital not only for engineers and designers but also for anyone who relies on these components in their daily operations. Whether it’s in automotive applications or industrial machines, knowing the fundamentals of their operation can lead to improved efficiency and longevity.
Applications in Automotive Industry
The automotive industry makes extensive use of push-pull cables due to their versatility and reliability. One of the most common applications is in the throttle control system. Here, push-pull cables allow drivers to accelerate and decelerate smoothly by transmitting their input from the accelerator pedal to the engine control system. The direct and responsive nature of these cables enhances the driving experience, making them a preferred choice for vehicle manufacturers.
In addition to throttle controls, push-pull cables are also used in various other automotive systems, such as hood releases, door latches, and even parking brakes. The ability to engage and disengage mechanisms with precision is crucial for safety and convenience. For instance, a malfunctioning hood release cable can lead to unsafe driving conditions, which is why proper maintenance and periodic inspections are recommended.
Another significant application of push-pull cables in the automotive sector is in the control of convertible roofs. These cables facilitate the smooth opening and closing of the roof, allowing drivers to enjoy the benefits of an open vehicle while also providing a secure closure when needed. Manufacturers often design these systems with durability in mind, ensuring that the cables can withstand the repeated stresses associated with daily use.
Moreover, as vehicles evolve with new technologies, the role of push-pull cables continues to adapt. With the rise of electric vehicles and advanced driver-assistance systems, these cables may be integrated into more complex electronic systems, requiring engineers to rethink their designs and applications. Understanding the current and future applications of push-pull cables in the automotive industry is essential for anyone involved in vehicle design or maintenance.
Industrial Uses and Benefits
Beyond the automotive sector, push-pull cables find extensive applications in various industrial settings. They are commonly used in machinery control systems, where precise movement is required to operate equipment effectively. For instance, in manufacturing plants, push-pull cables can control conveyor belts, robotic arms, and other machinery, allowing operators to manage workflows efficiently.
One of the significant benefits of using push-pull cables in industrial applications is their ability to operate in confined spaces. Their flexible design allows for installation in areas where rigid systems would be impractical. This adaptability is particularly advantageous in complex machinery layouts where space is at a premium.
Furthermore, push-pull cables require minimal maintenance compared to other mechanical systems. Their straightforward design and durable materials mean that they can endure harsh operating conditions without frequent replacement. This longevity can lead to cost savings for businesses, as fewer repairs and replacements are necessary over time.
Another advantage of push-pull cables in industrial applications is their ability to provide tactile feedback to operators. When engaged, these cables can offer a sense of resistance, allowing users to feel when a mechanism is activated. This feedback can be critical in ensuring that operators make accurate adjustments, enhancing both safety and efficiency in high-stakes environments.
In summary, the industrial use of push-pull cables showcases their versatility and reliability. Their ability to function effectively in various applications, coupled with their low maintenance needs, makes them invaluable in modern manufacturing and machinery operations.
Choosing the Right Push Pull Cable
Selecting the appropriate push-pull cable for a specific application involves considering several factors. The first step is to assess the required load and the environment in which the cable will operate. Different applications may demand varying levels of strength, flexibility, and durability, so understanding these needs is crucial.
Material selection is another vital aspect of choosing the right push-pull cable. Cables can be made from various materials, including stainless steel, nylon, and other synthetic compounds. Each material has its advantages and disadvantages, such as corrosion resistance, weight, and flexibility. For example, if the cable is to be used in a harsh outdoor environment, selecting a corrosion-resistant material will prolong its lifespan.
The length of the cable is also an important consideration. It must be long enough to reach the desired components without being so long that it becomes unwieldy or prone to tangling. Additionally, the cable’s end fittings should match the requirements of the mechanisms they will connect to, ensuring a secure and reliable connection.
Another factor to consider is the installation process. Some push-pull cables may require specific tools or techniques for proper installation, while others may be more straightforward. It’s essential to follow the manufacturer’s guidelines to ensure optimal performance and safety.
Lastly, consulting with manufacturers or suppliers can provide valuable insights into the best options available for your specific needs. They can offer recommendations based on their experience and the latest developments in push-pull cable technology.
In conclusion, choosing the right push-pull cable involves a careful analysis of various factors, including material, length, and installation requirements. Making informed decisions can lead to enhanced performance and reliability in any application.
In summary, push-pull cables are integral components in various industries, particularly in automotive and industrial applications. Their unique design allows for effective motion transfer, making them invaluable for precise control systems. Understanding their operation, applications, and selection criteria can help users maximize their functionality and efficiency.

