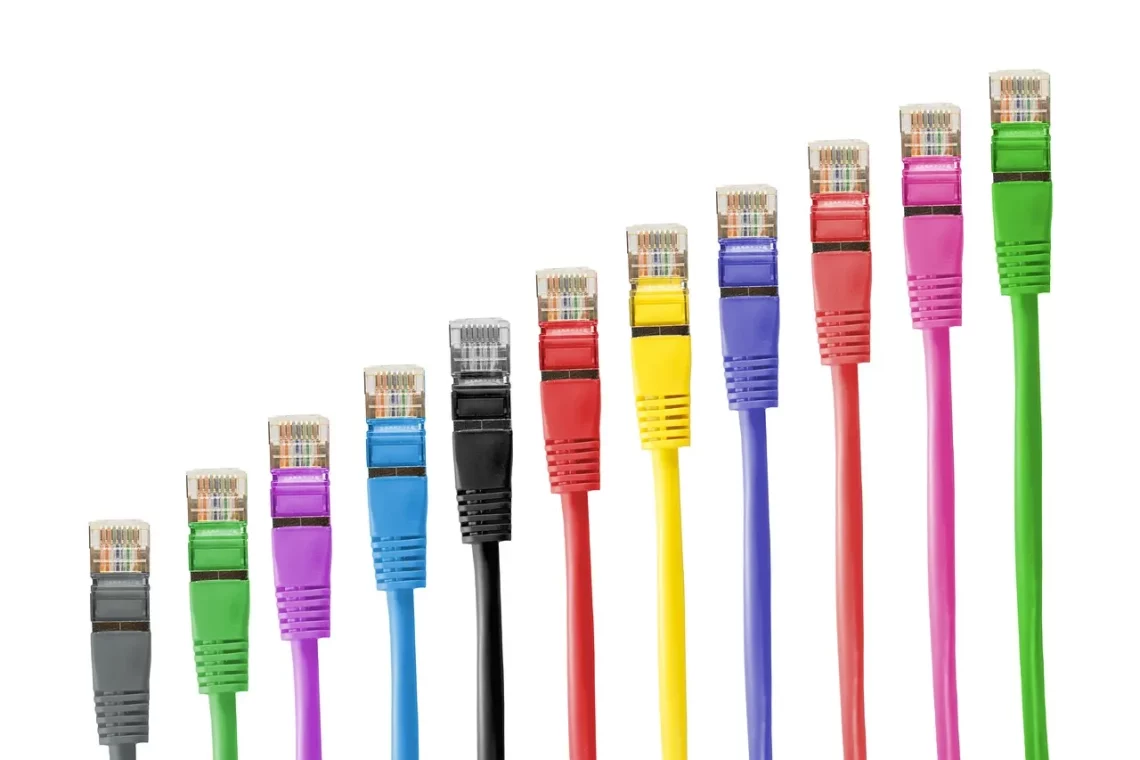
Understanding Push Pull Cables: Functionality and Applications Explained
Push pull cables are an integral part of various mechanical systems, playing a crucial role in the operation of numerous devices. These cables, which are designed to transmit force and motion, are utilized in a wide range of applications, from automotive to industrial machinery. Understanding the functionality of push pull cables is essential for anyone involved in engineering, maintenance, or design of mechanical systems.
At a fundamental level, push pull cables operate on the principle of transmitting linear motion. They consist of a flexible cable encased in a protective sheath, which can withstand environmental stressors while allowing smooth movement. The functionality of these cables is not just limited to transferring mechanical force; they also ensure precision and reliability in various operations. This makes them indispensable in applications where exact movements are critical.
The versatility of push pull cables can be seen in their diverse applications. They can be found in everyday items such as bicycle brakes, as well as complex systems like aircraft control mechanisms. Understanding how these cables work and the contexts in which they are used is vital for optimizing their performance and lifespan. In this article, we will delve deeper into the mechanics of push pull cables, their various types, and the industries that benefit from their unique properties.
How Push Pull Cables Work
Push pull cables operate on a straightforward principle of mechanical transmission. They consist of a flexible inner cable that slides through a rigid outer sheath. This configuration allows the inner cable to either push or pull, depending on the application. The basic components of a push pull cable include the core cable, the outer casing, and the end fittings, which connect the cable to the mechanisms they operate.
The inner cable is usually made of steel or other durable materials, providing the strength required to handle significant loads. The outer casing, often made from a polymer or metal, protects the inner cable from environmental damage while allowing for smooth movement. When a force is applied to one end of the cable, it transmits that force through the inner cable to the other end, resulting in linear motion.
One of the key advantages of push pull cables is their ability to function in confined spaces. They can be routed through tight areas without losing efficiency, making them ideal for applications in vehicles, machinery, and even household appliances. Their design allows for flexibility; they can be easily bent and shaped to fit specific configurations, which is essential in complex systems.
Moreover, push pull cables provide a tactile response, allowing users to feel the action being performed. Whether it’s the gentle squeeze of a bicycle brake lever or the precise movement of a control in an aircraft, the feedback provided by these cables enhances user experience and operational safety.
In summary, the functionality of push pull cables is centered around their ability to transmit motion effectively and reliably. Their design not only facilitates smooth operation in a variety of environments but also contributes to the safety and precision of the devices they serve.
Types of Push Pull Cables
Push pull cables come in several types, each designed for specific applications and requirements. The most common classifications include standard push pull cables, lockable cables, and adjustable cables. Understanding these variations is essential for selecting the right cable for a given application.
Standard push pull cables are the most widely used type. They are designed for general applications, where a simple push or pull motion is required. These cables are typically straightforward in design, allowing for easy installation and maintenance. They can be found in various applications, from automotive controls to industrial machines.
Lockable push pull cables feature a mechanism that allows the cable to be locked into place once it has been adjusted. This type is particularly useful in applications where the position needs to be secured, such as in throttle controls or adjustable seating systems. The locking mechanism prevents unintended movement, enhancing safety and stability.
Adjustable push pull cables offer the flexibility to change the length of the cable according to the needs of the application. This adaptability makes them ideal for systems that require frequent adjustments or varying distances. These cables are commonly used in systems like hydraulic controls, where precision is critical for safe operation.
In addition to these standard types, push pull cables can also be customized to meet specific requirements. This customization may include variations in length, materials, and end fittings, allowing for a tailored solution to unique mechanical challenges. Such flexibility is a significant advantage in industries where precision and reliability are paramount.
When selecting a push pull cable, it’s essential to consider the specific requirements of the application, including the load capacity, the environment in which it will operate, and any unique features that may be necessary. Choosing the right type of push pull cable can significantly impact the efficiency and effectiveness of the system in which it is used.
Applications of Push Pull Cables Across Industries
Push pull cables are utilized in an extensive range of industries, showcasing their versatility and reliability. From automotive engineering to aerospace applications, these cables play a critical role in ensuring the functionality of various systems.
In the automotive industry, push pull cables are commonly found in throttle controls, gear shifters, and brake systems. They allow for smooth and reliable operation, ensuring that drivers can control their vehicles efficiently. The tactile feedback provided by these cables enhances the driving experience, making them a preferred choice in modern vehicles.
In industrial settings, push pull cables are essential for operating machinery and equipment. They are commonly used in conveyor systems, cranes, and lifting equipment, where precise control is necessary for safety and efficiency. The ability to operate these systems remotely or in hard-to-reach places further emphasizes the importance of push pull cables in manufacturing and logistics.
The aerospace sector also benefits from the use of push pull cables, where they are employed in control surfaces for aircraft. These cables must meet strict regulatory standards due to safety concerns in aviation. Their reliability and precision are crucial for the safe operation of aircraft, making them indispensable in this high-stakes industry.
Moreover, push pull cables find applications in consumer products as well. They are used in items such as lawn mowers, bicycles, and even furniture. In these cases, the cables enhance user convenience and safety, allowing for easy adjustments and controls.
In conclusion, the applications of push pull cables are vast and varied, spanning multiple industries and products. Their reliability, versatility, and ability to provide precise control make them an invaluable component in both complex machinery and everyday items. Understanding their applications can help industries optimize their operations and improve overall functionality.
Maintenance and Best Practices for Push Pull Cables
Proper maintenance of push pull cables is essential to ensure their longevity and optimal performance. Regular checks and care can prevent potential failures and extend the lifespan of these critical components. Here are some best practices for maintaining push pull cables.
First and foremost, regular inspection is key. Users should check for signs of wear, fraying, or corrosion, especially in high-use applications. The outer casing should also be examined for any damage that could expose the inner cable to environmental elements. Early detection of wear can prevent more significant issues down the line.
Lubrication is another important aspect of maintenance. Keeping the inner cable lubricated ensures smooth movement within the outer sheath, reducing friction and wear. Appropriate lubricants should be used, and care must be taken to avoid over-lubrication, which can attract dirt and debris, leading to more wear.
Another best practice is to ensure that the cable is installed correctly. Misalignment or improper routing can lead to premature wear and failure. Following the manufacturer’s guidelines for installation can help mitigate these risks. Additionally, ensuring that the cable is not subjected to excessive bending or stress during operation is crucial for its longevity.
Finally, users should be aware of the environmental conditions in which the cables operate. Extreme temperatures, humidity, or exposure to chemicals can all affect the performance and lifespan of push pull cables. Selecting materials designed for specific environments can help enhance their durability and reliability.
In conclusion, maintaining push pull cables through regular inspections, appropriate lubrication, proper installation, and environmental awareness can significantly enhance their performance and lifespan. Implementing these best practices is essential for any operation relying on these critical components.
By understanding the functionality, types, applications, and maintenance of push pull cables, users can ensure optimal performance and safety in various mechanical systems. Whether in automotive, industrial, or consumer applications, these cables remain a vital element in the efficient operation of machinery and devices.

