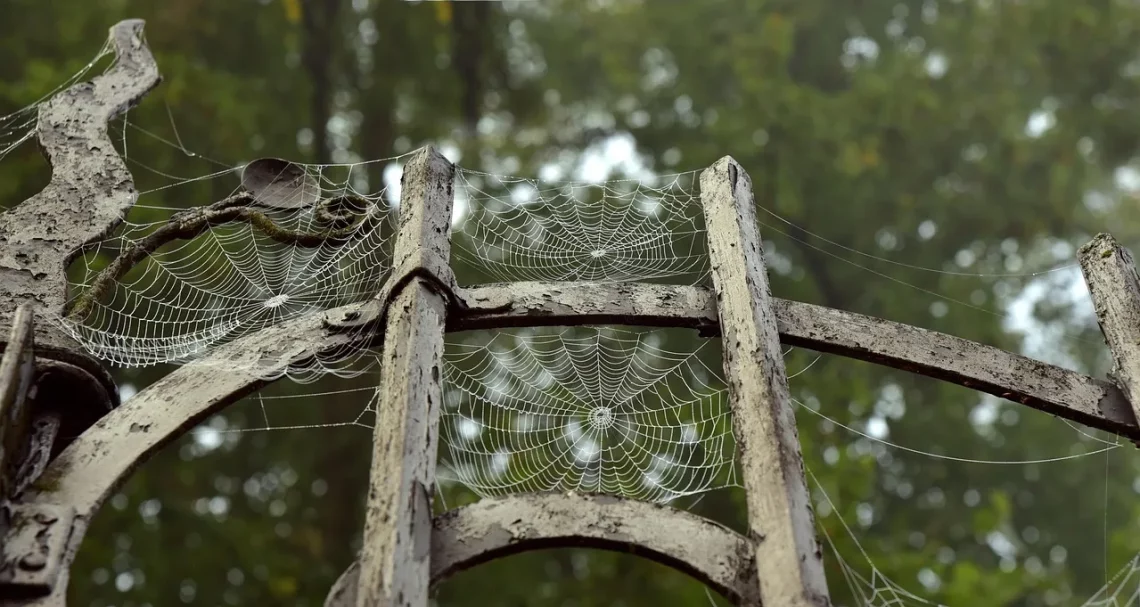
Jenkins Innovations in Iron and Steel Production Processes
The iron and steel industry plays a crucial role in the global economy, serving as a foundation for various sectors, including construction, automotive, and manufacturing. Over the years, this industry has undergone significant transformations driven by technological advancements and the need for sustainable practices. Innovations in production processes have not only enhanced efficiency but also addressed environmental concerns associated with traditional methods. As industries strive for greener solutions, the emphasis on adopting cutting-edge technologies has become paramount.
The use of automation, artificial intelligence, and data analytics has emerged as a game-changer in optimizing production efficiency and reducing waste. Moreover, these innovations have propelled the industry into a new era, where adaptability and responsiveness to market demands are vital. As companies navigate the complexities of modern manufacturing, understanding the latest trends and technologies is essential for maintaining competitiveness.
In this context, exploring the advancements and innovations in iron and steel production processes reveals not only their significance for manufacturers but also their broader impact on sustainability and environmental stewardship. This discussion highlights the intersection of technology and industry, showcasing how these developments are reshaping the landscape of metal production.
Automation and Smart Manufacturing
Automation has revolutionized the iron and steel production processes, significantly improving operational efficiency and safety. By integrating robotics and automated systems, manufacturers can streamline various stages of production, from raw material handling to final product delivery. Automated systems reduce the risk of human error, enhance precision, and ensure consistency in output quality.
Smart manufacturing, which leverages the Internet of Things (IoT) and advanced analytics, is another significant trend in the industry. With interconnected machines and sensors collecting real-time data, manufacturers can monitor processes continuously, facilitating predictive maintenance and minimizing downtime. This data-driven approach empowers companies to optimize production schedules and resource allocation, ultimately leading to cost savings and increased productivity.
Moreover, automation and smart manufacturing contribute to enhanced safety measures. By deploying robots for hazardous tasks, manufacturers can protect their workforce from potential risks associated with heavy lifting, exposure to high temperatures, and harmful substances. This shift not only fosters a safer working environment but also allows skilled labor to focus on more complex and value-added activities.
As the demand for customized products increases, automation also enables greater flexibility in production. Manufacturers can quickly adjust their processes to accommodate varying specifications, ultimately improving customer satisfaction. This adaptability is crucial in a market where consumer preferences are continually evolving, and the ability to respond swiftly can provide a competitive edge.
In conclusion, the integration of automation and smart manufacturing in iron and steel production is a transformative trend that enhances efficiency, safety, and flexibility. As the industry continues to evolve, embracing these technologies will be essential for manufacturers seeking to thrive in a rapidly changing landscape.
Environmental Sustainability and Green Technologies
The iron and steel industry is often scrutinized for its environmental impact, particularly concerning greenhouse gas emissions and resource depletion. However, recent innovations have led to the development of greener technologies that aim to mitigate these challenges. The adoption of sustainable practices not only addresses regulatory pressures but also meets the growing demand from consumers for environmentally friendly products.
One notable advancement is the use of alternative energy sources in production processes. Traditional methods predominantly rely on fossil fuels, contributing to pollution and carbon emissions. In contrast, the incorporation of renewable energy, such as wind or solar power, can significantly reduce the carbon footprint associated with iron and steel manufacturing. This shift not only aligns with global sustainability goals but also positions companies as responsible corporate citizens.
Additionally, innovations in recycling and circular economy practices are gaining traction within the industry. By promoting the reuse of scrap metal and optimizing recycling processes, manufacturers can reduce the reliance on virgin materials. This not only conserves natural resources but also minimizes energy consumption, as recycling typically requires less energy than primary production.
Furthermore, advancements in carbon capture and storage (CCS) technologies are being explored to address emissions directly at the source. By capturing CO2 produced during the production process and storing it underground, companies can significantly lower their overall emissions. While still in the development phase, these technologies hold promise for creating a more sustainable future for iron and steel manufacturing.
Ultimately, the integration of environmental sustainability and green technologies within the iron and steel industry is essential for addressing the pressing challenges of climate change. As manufacturers continue to innovate and invest in sustainable practices, they contribute to a more responsible and eco-friendly future for the sector.
Digital Transformation and Data Analytics
Digital transformation is a critical trend reshaping the iron and steel production landscape. By harnessing the power of data analytics, manufacturers can gain valuable insights into their operations, leading to enhanced decision-making and improved performance. The ability to analyze vast amounts of data collected from various sources enables companies to identify inefficiencies, optimize processes, and reduce costs.
One of the primary applications of data analytics in iron and steel production is predictive maintenance. By analyzing equipment performance data, manufacturers can forecast potential failures before they occur, allowing for timely interventions. This proactive approach minimizes downtime, extends equipment lifespan, and ultimately boosts productivity.
Moreover, data analytics can enhance supply chain management. By leveraging real-time data, manufacturers can optimize inventory levels, streamline procurement processes, and improve logistics. This not only reduces operational costs but also ensures that production schedules align with market demand, minimizing excess inventory and waste.
Additionally, the integration of machine learning and artificial intelligence (AI) into data analytics further enhances the industry’s capabilities. These technologies can identify patterns and trends that may not be immediately apparent, enabling manufacturers to make informed decisions based on predictive models. This level of insight empowers companies to adapt their strategies dynamically, ensuring they remain competitive in a rapidly evolving market.
As digital transformation continues to unfold, the iron and steel industry must embrace these changes to stay relevant. The ability to leverage data effectively is no longer optional; it is a necessity for manufacturers aiming to thrive in a technology-driven world. By investing in digital tools and fostering a culture of innovation, companies can position themselves for long-term success.
Collaboration and Industry Partnerships
Collaboration and partnerships within the iron and steel sector are becoming increasingly vital as companies navigate the complexities of modern manufacturing. The challenges posed by globalization, technological advancements, and sustainability goals necessitate a collective approach. By working together, manufacturers can share knowledge, resources, and best practices, driving innovation and efficiency across the industry.
Industry partnerships often facilitate research and development initiatives, allowing companies to pool their expertise and resources. Collaborating with academic institutions, research organizations, and technology providers can accelerate the development of new processes and technologies. These partnerships foster a culture of innovation, enabling manufacturers to stay ahead of the curve and adapt to changing market demands.
Moreover, collaborations can extend beyond technological advancements to include sustainability efforts. By working together, companies can implement industry-wide initiatives aimed at reducing environmental impact and promoting responsible practices. This collective approach can lead to the establishment of standards and benchmarks that drive improvements across the sector.
Furthermore, collaboration with stakeholders, including suppliers, customers, and regulatory bodies, is essential for fostering transparency and accountability. Engaging with these groups allows manufacturers to understand market expectations and align their practices accordingly. This stakeholder engagement not only enhances brand reputation but also builds trust and loyalty among consumers.
In conclusion, collaboration and industry partnerships play a crucial role in the ongoing evolution of the iron and steel sector. By leveraging collective expertise and resources, manufacturers can drive innovation, enhance sustainability, and navigate the challenges of a rapidly changing landscape. Embracing collaboration will be key to unlocking new opportunities and ensuring the industry’s long-term viability.

